How intelligent furniture design can solve the fitter shortage
Business consultant at Kbbsupport.com Toby Griffin says the design of kitchen furniture could help circumnavigate an installer shortage – and here’s how.
Business consultant at Kbbsupport.com Toby Griffin says the design of kitchen furniture could help circumnavigate an installer shortage – and here’s how.
Here’s a controversial opinion: perhaps we don’t have a looming crisis in the shortage of kitchen fitters?
Before you start getting hot under the collar, bear with me for a bit. In June I gave a talk to a good-sized audience at The Kitchens of the Future presentation stand at The Installer Show entitled ‘Off-The-Shelf versus Custom-Made kitchens’.
Sponsored Video
In it, I discussed how all the big-boys in the kitchen retail industry sell standard cabinetry, despite there being over 1,000 independent factories in the UK capable of making custom-sized furniture. So what (you may ask)?
Well, talking as I do on a regular basis to kitchen fitters, most love custom-sized cabinetry, because it makes the installation much quicker. In fact I’ve been given numbers of around a 40% time saving on site, as there is a fraction of the cutting, screwing, re-sizing, frontal fitting, mechanism/drawer fitting, etc.
There’s even a reduced requirement for panelling in many designs, as the carcases can be built to co-ordinate with the colour of the doors.
So let’s ‘do the maths’ here. If a kitchen normally takes a week to fit – but with custom-made products can be fitted in 40% less time – over a two-week period, instead of installing two, a fitter can complete three, and have a day off!
Therefore the same labour force of installers could install 50% more kitchens.
Advantages of custom
But, you may say, custom kitchens are like bespoke kitchens, and are way out of the budget of most clients. It seems that this is not true.
A custom kitchen (by which I don’t mean a bespoke kitchen with unique colours, and special pieces) is generally competitively priced against the national brands, which surprises most installers and end-clients.
So why aren’t all kitchens made in this way then?
Well, custom-made furniture is not ‘a bed of roses’, and requires much more thought and preparation than off-the-shelf.
With products being made specifically for each client/project accurate measurements are required, plans need to be checked with issues highlighted and resolved by smart order-processors and lead-times – generally of two weeks for a UK manufacturer – are required from order to delivery.
What about remedials then?
Being able grab a length of plinth at the last minute to get a job finished is definitely handy, but most smaller factories can quickly fly through a panel, plinth, carcase in 24 hours, so there’s not a big wait, and it’d be made exactly to size too, so quicker and easier to fit.
All of the above cuts down on waste product too (of course better for the wallet, the environment, and disposal), brings more skilled employment to the local factories.
In addition, it makes for a happier end-client as they don’t have a fitter camped out in their home for ages, and the finish is improved as a factory cut’n’edge is generally better than one done on site.
Shift workloads
In conclusion then, I believe that the crisis of kitchen installers could – in part at least – be avoided by reducing the work done by the fitter on site, and shifting it to the offices and factory of the kitchen supplier.
I understand that this will upset the model of many of the country’s biggest manufacturers, but it can – and perhaps must – be done to keep this industry from withering due to a skilled kitchen installer shortage.
Related Articles
#socialwall
Sintered stone manufacturer Neolith has launched Calacatta Roma and Cappadocia Sunset, inspired by nature and classical architecture, and for use in kitchens or bathrooms walls, floors, in gardens or facades.
They belong to The New Classtone and Fusioncollections which interpret marble and natural stone, respectively, and boast Neolith’s antibacterial NeolEAT technology.
Inspired by Ancient Rome, Calacatta Roma (pictured top) pays homage to Italian Carrara marble, with ochre and grey veins in a white background.
While the Cappadocia region, in central Turkey, with its rock formations formed by volcanoes and underground cities, has inspired Cappadocia Sunset (pictured below).
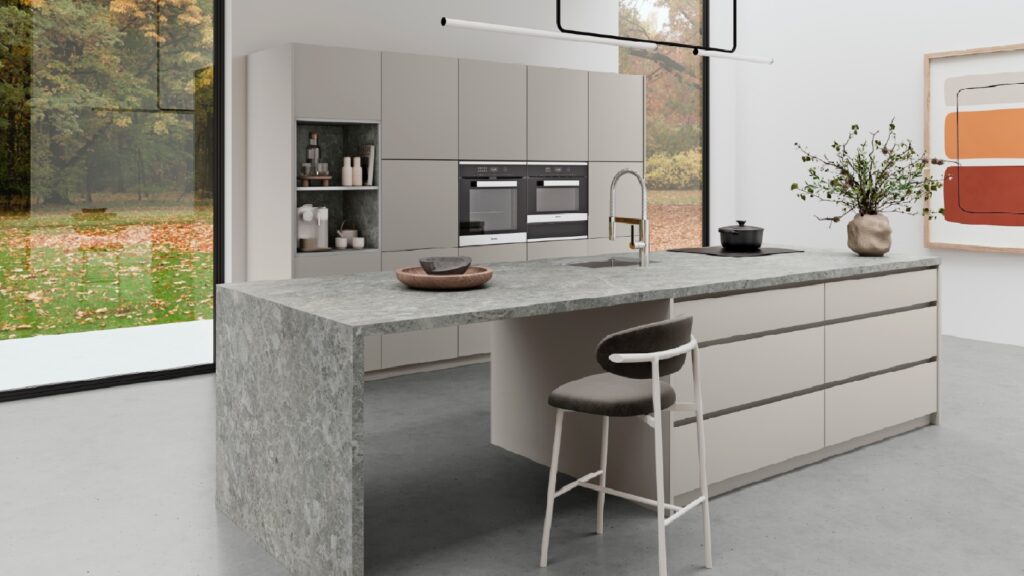
Just like all of Neolith’s surfaces, Calacatta Roma and Cappadocia Sunset are resistant to heat and atmospheric conditions, are 100% recyclable, and do not contain added quartz to their formulation.
Mar 14, 2024
JUST OUT: @AcquabellaBath has unveiled a choice of shower grate patterns for its Base and Arq shower trays… https://t.co/kMN83c40Qf
JUST OUT: @FrankeUK unveils Mythos single lever mixers in Swivel Spout and Pull-out Nozzle options. #kitchendesign https://t.co/TSKCAo5r0e
INTERVIEW: Sales and marketing director of @blumuk David Sanders on how the kitchen industry has changed post-pand… https://t.co/k9LIpUhhDF
NEWS: Challenging housing market is driving home improvements, finds new research by @HafeleUK #HomeImprovement… https://t.co/eMB7jludIm
NEWS: British manufacturer @kudosshowersltd acquired by European SanSwiss. #acquisition #manufacturers #bathrooms https://t.co/gpOv7jMevn
NEWS: @HafeleUK announces Richard Curtis as managing director. #newhire #appointment #leadership https://t.co/NP8U5ramOb
NEWS: @officialbikbbi names CT1 sealant manufacturer as corporate sponsor. #installation #installer https://t.co/8zsxs2HI3n
NEWS: @quookeruk named one of fastest-growing companies in North West. #business #Awards https://t.co/9zZ1ZDGrFI
RETAILER FOCUS: Managing director and design director of UK Kitchen Retailer of the Year @KitchensbyJSG Jim Geddes… https://t.co/JhL3vmxwbd
NEWS: Consumers are renovating for long term, with kitchens and bathrooms a priority, finds @HouzzUK… https://t.co/9VhoTUDI0B
PROFILE: Managing Director of Flair Showers Alan Wright talks about the relaunch of the company, creation of a Show… https://t.co/WDMPqDt2Uk
The new @blumuk carbon black LEGRABOX boasts beautifully slim drawer sides, bringing furniture onto trend, easily b… https://t.co/DrEXXWTyQb
NEWS: House of Fraser owner @FrasersGroupPLC enters strategic partnership with @ao, buying a stake in the online e… https://t.co/44N0O9bekn
NEWS: @HowdensJoinery awarded @WhichUK Best Buy for its rigid cabinets and handleless kitchens. #kitchen… https://t.co/rALz8XRHbv
NEWS: @grohe invites 800 guests from around the world to its Grohe X Professional event in Lisbon, Portugal.… https://t.co/2RGjDum980
JUST OUT: Home appliance brand Candy has unveiled the Rapido dishwasher, claimed to be the fastest and most spaciou… https://t.co/mbWn2pJp2C
Newsletter
Sign up to receive our newsletter and we’ll send you details of our latest videos, competitions and much more